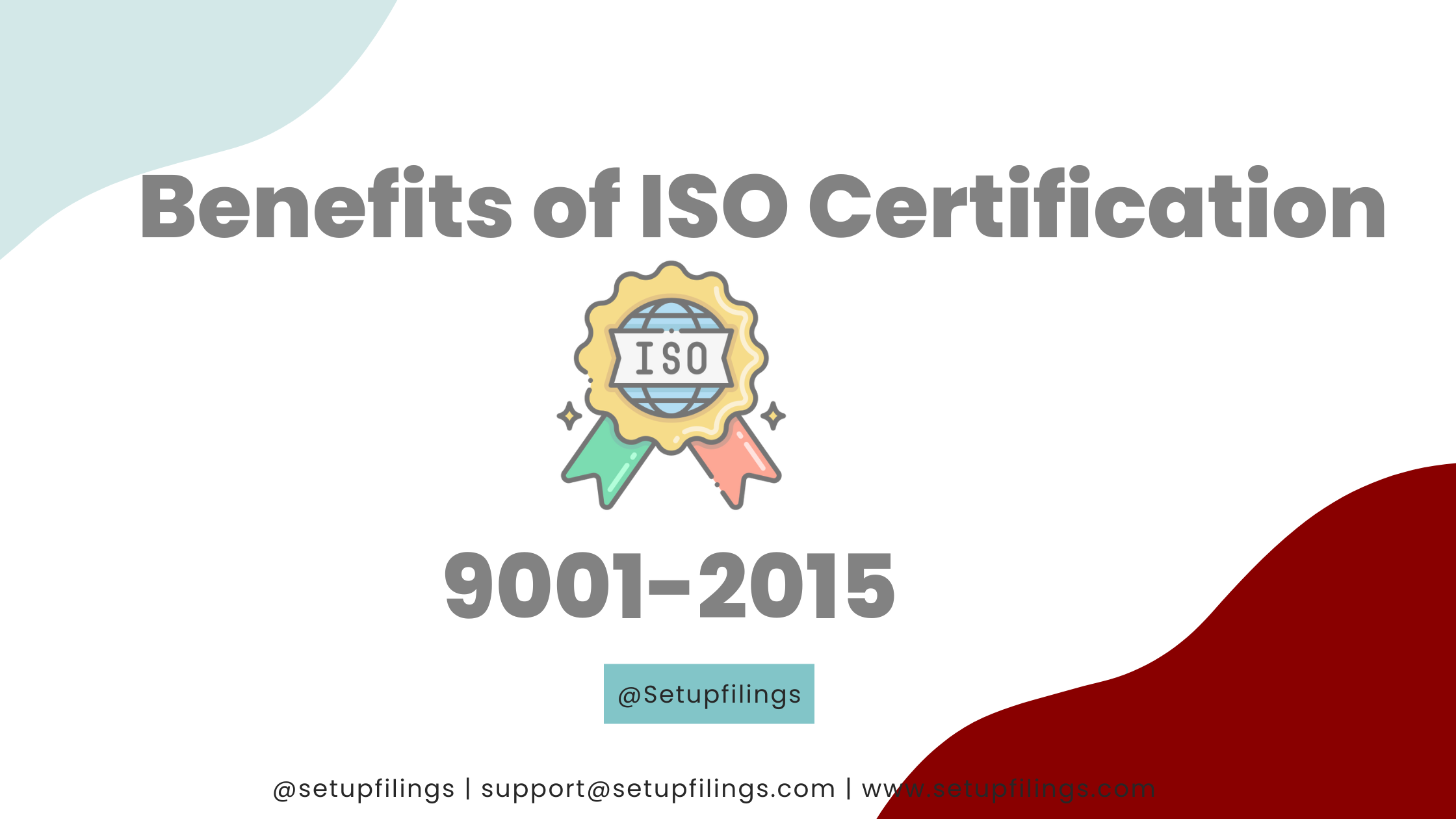
Unlock the Benefits of ISO 9001: Improve Efficiency & Quality
There are numerous advantages to obtaining ISO 9001 certification. ISO 9001 is a global standard that defines the requirements for a quality management system (QMS). Companies become certified to demonstrate their capacity to consistently supply products and services that fulfill the needs of their customers and the standards of the regulatory authorities. ISO 9001 provides assistance for your team and customer satisfaction whether you choose to become certified or are compelled to become certified.
Changes in management will always put additional strain on your company, but the benefits of implementing the ISO 9001:2015 Quality Management System (QMS) are well worth the effort as you move forward.
Blueprints are one of many items rendered obsolete by technology and electronic information. Establishing a QMS (such as ISO 9001) is similar – a little work up front, but the benefits of ISO in your firm will be obvious after a short period.
Regardless of your certification, we strongly advise you to adhere to the Seven Quality Management Principles (QMPs) in order to reap the full benefits of ISO 9001.
10 Benefits of ISO 9001
The following are the ten advantages of ISO 9001:2015 quality management systems:
Improved Efficiency: Before undergoing the ISO 9000 series Quality Management Standards certification procedure, the companies conducted considerable research on the processes they use, as well as how to maximize equity and efficiency. The processes are established once they are certified. There are principles that anyone can readily follow, making it simple to provide training, transfers, and even troubleshooting.
Increased Revenue: It has been noticed that ISO QMS certified organizations outperform uncertified companies in terms of productivity and financial performance.
Employee Morale: Employees are more satisfied and motivated when there are defined roles and duties, management accountability, a well-established training program, and a clear understanding of how employees’ roles affect quality and the overall performance of the organization.
International Recognition: The International Organization for Standardization (ISO) is widely regarded as the quality management authority on a global scale.
Factual Decision Making: The ISO9000 QMS standard includes detailed instructions for audits and process evaluations. This aids in information collecting and data-driven decision making.
Supplier Relationships: ISO certification has been shown to be advantageous in terms of supplier relationships. The documentation and testing methods aid in ensuring the quality of the raw materials used in manufacturing. This also aids in thoroughly assessing a new supplier before switching vendors. There is a mechanism in place to ensure uniformity in how and where orders are placed.
Documentation: Because the ISO QMS standard demands proper documentation of all operations, modifications performed, faults or discrepancies, it aids in problem mitigation and provides stability. The employees are also more accountable. Documentation also ensures that traceable records are available in the event that non-compliant goods or raw materials are used.
Consistency: Because all processes are recorded, errors are kept to a minimum. The processes are extensively documented, beginning with research and development and continuing through production and shipment. Even minor changes to the process must be recorded to ensure that the changes are adequately planned and handled in the most efficient manner feasible.
Consumer Satisfaction: Because ISO is a globally recognized standard, businesses may easily acquire the trust of their customers. ISO9001 QMS accreditation guarantees that firms provide efficient, consistent, and dedicated quality service, assuring customer satisfaction.
Process Improvement: The ISO 9000 QMS focuses on audit processes, management reviews, and improved processes based on data obtained. Improvements are carefully planned and performed based on facts and using a system of documentation and analysis. This guarantees that the right decisions for your organization are taken.
Want to learn more about the ISO 9001 Benefits?
Read about ISO 10014 Quality Management Guidelines and how to use them to reap the financial and economic benefits of ISO 9001.
What is the return on investment for ISO 9001?
ISO 9001:2015 ROI can be demonstrated in a variety of areas of your firm, from an increase in customers to a decrease in waste. The return on investment will change based on the industry. Companies are often enjoying a gain in revenue, a decrease in costs, and an increase in profit. The following data demonstrate the advantages of ISO 9001:
- 72% of Companies with ISO 9001 report a significant competitive advantage. That is, since deploying the QMS, they have gained more business.
- 33% of ISO 9001-certified businesses reported an increase in consumer demand.
- 69% of non-ISO 9001 firms report they have lost a customer bid or proposal to a rival who is an ISO 9001:2015 certified customer.
- 35-40% of businesses said their competitors are ISO 9001:2015 certified or are in the process of being certified. As ISO 9001 evolves, so will your competitors, causing you to fall farther behind.
ISO 9001 Certification for Top Management and Workers
Another significant advantage of ISO 9001 certification is company involvement. When you decide to implement the ISO 9001 Standard in your firm, the standards necessitate greater participation from top management, and your overall Quality Management System will improve.
- This starts with the setting of the Quality Policy and Quality Goals and Objectives.
- It continues with Management Review looking at data from the QMS, and taking actions to make sure that Quality Goals are met.
- New Goals are set, and continual improvement is achieved.
- With the QMS in place and working for you, the organization is focused towards the Quality Goals.
- Management is provided with data on a continual basis and able to see progress or lack of progress towards goals and take appropriate action.
- The organized, scheduled process of conducting Management Review ensures that this evaluation takes place.
- It provides a method for regularly reviewing goals and performance versus goals, as well as taking action based on the evaluation.
Improved productivity is the consequence of the initial examination and improvement of procedures that occurs during the implementation phase, as well as enhanced personnel training and qualification.
- Improved process documentation or control (for example, establishing and adhering to a written quality manual) leads to consistency in performance and fewer scrap and rework.
- Managers receive fewer late-night troubleshooting calls, and employees have more information to solve problems on their own.
ISO 9001 for Customer Satisfaction
• Another significant advantage of ISO 9001 is increased customer satisfaction. Customer satisfaction rises as goals and objectives consider the demands of the consumer.
• As customer input is sought, received, and analyzed, consumer demands are better understood.
• Based on the information, goals and objectives are altered, and the organization becomes more customer-focused.
• As goals become more customer-focused, the company spends less time focusing on individual department goals and more time collaborating to address customer needs.
All of this results in financial gains. According to studies, investing money on prevention is much less expensive than addressing an issue after a product or service has been delivered to a customer. Simulations have shown that the costs increase tenfold when moving from preventative to external failure costs. That is, it will cost your business around ten times as much to deal with an issue once it has reached a customer as it would to deal with it in-house, and it will cost a tenth to prevent the issue in the first place.
Visited 191 Times, 2 Visits today